We are Manufacturer, Supplier, Exporter of Tank Bottom Ball Valves, Flush Bottom Ball Valve For Tank and Reactors. Our setup is situated in Pune, Maharashtra, India.
- Low sump area
- Cavity free
- Full bore
- Direct mounting to vessel flange
- Unique push fit design (easy maintainability/ low torque)
- Angled stem design
- Double sealing of vessel flange
- One piece body design
- Adjustable and maintenance free stem sealing with additional O-ring
Design Per Customer Requirements:
- Metal to metal sealing system for high pressure, high temperature and abrasive operating conditions
- Ball valve design customizable to special vessel flanges
- Bottom vessel flange contour can be adapted to vessel shape.
- Heating jacket
- Flushing connection
- Extended stem
- Double packed stuffing box design
- Antistatic- Design
- Scraper chamfer for cutting viscous product
Leakage Test:
- Vessel bottom flange acct. to DIN28117/28140
- Special connection as per customers’ request
Leakage Test:
- Acc. To EN 12266-1 leak rate A
Actuator mounting flange:
- DIN/ISO 5211
ADVANTAGES
SANKEY METAL SEATED BALL VALVE
Metal to Metal Seating
The ball and the seat rings are hard-faced on the sealing areas by using different coatings selected upon the service conditions i.e. Electro-less Nickel Plating, Stellite hard facing, Chromium Carbide and above all Tungsten Carbide which assures, per our experience, the best results in most applications. The sealing is assured by true metal to metal contact between the two hard-coated surface. Each coating is applied per specific methodologies, i.e. Tungsten Carbide is applied by high velocity detonation gun.
Stem Design
The stem is independent from the ball and is a blowout proof design. The stem seals are designed per the service conditions, i.e. for high temperature valves (above 250 degC) stem seals is composed of loaded graphite packing. Valves for high temperature conditions are designed with extended stem to maintain the maximum sealing capacity of the packing.
TYPE : | Single Piece cavity filler Flanged End |
PORT : | Full Bore |
SIZE : | 15 mm to 250mm NB |
Pressure Rating : | ASME #150 PN 20
ASME #300 PN 50
ASME #600 PN 100
|
Temperature Range | 35 Deg C to 280 Deg C (Soft Seated) |
Body Materials | Stainless Steel / Carbon Steel / Alloys |
Design Standard | ISO 17292 rev 2004 |
End Flanges | ASME B16.5 2013 |
Face to Face Dimension | Non-Standard (As per Manufacturer) |
Fire safe design | API-607 Rev 2010 |
Testing | API 598 Rev 2009 |
Sour Service | NACE MOR 0175 Rev 2009 |
Documents | BS/EN 10204-3.1 REV 2004 |
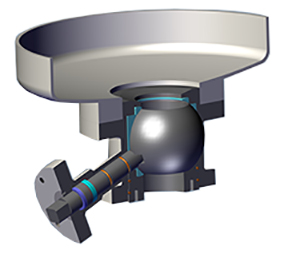
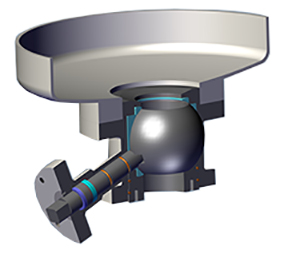
The SANKEY TBV series flush bottom tank ball valve incorporates all the benefits of ball valve negating the disadvantages of conventional flush tank valve. Our Sankey TBV series valve incorporates the geometric design of the mounting Pad, which is welded to the tank, allowing a smooth flow and prevent stagnating of the media.
Our Valves offer the best solution:
- Where minimum Dead Space between ball and tank is required.
- Where media could stagnate at tank outlet.
- Where Full blending of reactor volume is imperative.
Advantage over a conventional tank bottom valve
- Higher CV
- Direct Flow
- Simple Quarter turn operation (Easy automation)
- Low weight and compact
- Easy maintenance
Valve Application: Filter dryer / vacuum dryer / Stirrer vessel / Transport vessels / Reactor / Other vessel
Areas of application: Chemical / Pharmaceutical / Food / Cosmetics
Media: Gases / Fluids / Emulsion / Syrup / Paint / Food Product (Chocolate etc.) / Granulate material / Powder.
ADVANTAGES
SANKEY Tank Bottom Ball Valve
Low sump area
By the use of an angled stem design and the direct mounting to the vessel bottom flange, the ATEC bottom outlet ball valve ensures flush fitting with the vessel inner bottom.
- Minimal accumulation of product between ball valve ball and vessel inner bottom
- Improvement of product mixing in stirrer vessel
- Reduction of efflorescence and product agglomeration
- Avoiding false samples
Cavity free
The usual cavity between ball and housing in non- cavity free ball valves give cause for disturbance because residual products can crystallize, polymerize and so affect the function.
- Clean, non- false product
- No sediments of expensive products in the ball valve housing
Angled stem design
Because of the further distance from the actuator mounting flange to the vessel, it makes the automation of the ball valve and isolation of the vessel very convenient.
Direct mounting to vessel flange
The ball valve is mounted directly using screws or bolts to the vessel flange.
• Direct and easy assembly of ball valve to the container flange
TANK BOTTOM BALL VALVE
Sr.No. | PART NAME | STAINLESS STEEL | CARBON STEEL | QTY |
---|---|---|---|---|
1 | BODY | ASTM A351 CF8M | ASTM A216 Gr WCB | 1 |
2 | INSERT | ASTM A479 SS316 | ASTM A216 Gr WCB | 1 |
3 | BALL | ASTM A182 SS316 | ASTM A182 SS316 | 1 |
4 | STEM | ASTM A182 SS316 | ASTM A182 SS316 | 1 |
5 | SEAT | PTFE | PTFE | 2 |
6 | STEM SEAL | GRAPHITE | GRAPHITE | 1 |
7 | GLAND | SS316 | MS | 1 |
8 | STEM THRUST WASHER | GFT | GFT | 1 |
9 | STEM O-RING | VITON | VITON | 2 |
10 | END CONN. O-RING | VITON | VITON | 2 |
11 | CAVITY 1 | PTFE | PTFE | 1 |
12 | CAVITY 2 | PTFE | PTFE | 1 |
13 | LEVER | SS410 | SS410 | 1 |
14 | STOPER | MS | MS | 1 |